联系我们
地址:暂无
手机/微信一:15524700779
手机/微信二:13654200914
QQ客服一:暂无
QQ客服二:暂无
手机/微信一:15524700779
手机/微信二:13654200914
QQ客服一:暂无
QQ客服二:暂无
产品知识
提高电子铝箔质量的研究
日期:2017-08-02 人气:
内容提示: 文章来源于LW2016论文集——作者张安乐,何玉枝,刘雪梅(洛阳龙鼎铝业有限公司,河南 洛阳 471300) 随着人们生活的不断提高,铝制品在我们生活中也越来越广泛…
文章来源于LW2016论文集——作者张安乐,何玉枝,刘雪梅(洛阳龙鼎铝业有限公司,河南 洛阳 471300)
随着人们生活的不断提高,铝制品在我们生活中也越来越广泛,提高电子铝箔质量的问题尤其重要。电子铝箔的生产过程只要分为压延和精整两部分。近几年市场对电子铝箔的要求逐渐向更高质量和更大差异两方面转变,以清洗,剪切,复卷,退火等工序代表的精整技术开始变得非常重要,涉及到稳定并提高产品质量和提高企业满足客户差异需求的能力的大问题,成为了企业生存和发展必须面对的关键问题。
1 铝箔表面存在的缺陷
1.1 压坑
铝箔被清洗干净后必须惊醒烘干处理,由于轧制机和清洗剂易燃易爆物,其燃点在200℃左右。压坑是在烘干过程中,铝箔被风道、换热器、烘干箱等焊接体内剥离产生的固体颗粒割伤小的颗粒被卷入钢辊和铝箔之间后一般在箔面形成凹凸缺陷,降低产品质量;大的颗粒甚至会割穿箔面,造成报废
1.2 油斑
铝箔在清洗、漂洗的过程中,喷嘴将清洗剂通过一定的压力和流量喷射到箔面,清洗剂达到箔面并反弹到四壁后会产生大量高浓度的油雾,久而久之就形成了油斑。
1.3 擦伤
1.4 皱折
进入清洗道次的电子铝箔厚度一般在0.1mm左右,由于来料很薄,版型波动大,中浪和变浪等问题的出现,清洗过程中料在通过夹送辊和挤干辊时会出现皱折。
2 改善箔面的措施
2.1 压坑的改善措施
压坑的控制分为前期设备只在和后期的维护使用两步。烘干设备的高温氧化是不可避免的,但是在前期的设备制造过程中选用耐氧化的不锈钢材质,并采用氩弧焊等保护性气体焊接工艺,可能减少以后在使用中材质表面和焊接部位氧化的可能性。后期使用时在风道中增加多层不锈钢滤网,为了减少滤网堵塞降低风量,可将滤网定期清洗或更换列入日常维护。
2.2 油斑的改善措施
铝箔在清洗、漂洗过程中,箱体内会产生大量高浓度的油雾最终落在箔面上造成污染。由于大量排雾会消耗清洗剂,增加企业成本,且效果不理想,因此只能考虑阻挡油滴到箔面。发现油滴主要是在挤干辊至漂洗箱这段距离内在箱提顶部安装弧型挡板,并在漂洗箱出口顶部安装接油槽,将油滴引到两侧,即可消除箔面油斑。
2.3 擦划伤的改善措施
擦划伤产生的原因有机械结构、电器控制和工艺选用等三方面。
①对于各辊不同步可检查同步齿形带是否松紧合适,轴承是否润滑到位;
②电气调整电机参数使各个主动辊不同步,校正卷径误差控制方式选取简单的张力控制和速度控制。
③ 工艺张力和速度设置应与前后道次相匹配,选取最合理的范围。
2.4 皱折的改善措施
对于版型差的料,采取了以下措施:1.在开卷、卷取两侧增加几组S型U型辊起到校正作用;2.在开卷、卷取两侧安装板型调整辊。通过调整该辊的水平度和平行度消除边浪;3.通过增大胶辊或其它的凸度消除中浪。
3 电子铝箔的清洗
3.1 现状分析
3.1.1清洗的重要性
电子铝箔属于深加工技术,表面质量对电子存储能力的影响较大前一道工序在铝箔表面造成的微小缺陷会在后续工序中被放大,因此,只有在生产环节中的每道工序对箔面质量进行严格控制。
3.1.2清洗的过程
铝箔的清洗过程如下:带材从开卷机、入口偏导辊进入此装置,首先经过下刷辊,在下刷辊与带材之间喷有清洗液,洗刷带材下表面。接着,带材经过上级辊,在上级辊与带材之间也喷有清洗液,洗刷带材上表面。然后带材进入漂洗箱。还是使用同一种清洗液喷洗带材的上下表面。在经过2#剂干辊将带材表面的清洗油挤干。带材出漂洗箱后进入烘干箱,带材上残余的清洗液在热风的吹扫下被蒸发。最后,带材通过出口偏导辊后被卷取机争气地绕成卷。清洗结束。
4 电子铝箔的剪切
4.1 设备和质量缺陷现状的描述
剪切机是有不同型号的,这些设备中既有窄幅也有宽幅,既有切边也有抽条,既有单轴也有双轴,无论什么型号的剪切机主要由开卷、分 切、卷取三部分组成。随着客户对铝箔卷的需求向大卷重、高品质、短交货期、多规格变化。剪切机的刀、 轴、辊、管芯等部件都面临磨损加重、精度降低、更换频繁等问题。 剪切部分由于圆盘刀和刀垫的制作与配合精度问题会造成擦划伤、压坑、毛刺等质量缺陷。卷取部分由于面压辊、卷取轴和管芯的使用与设计问题会造 成翻边、错层、内应力不稳定等质量缺陷。
4.2 剪切的质量缺陷产生原因及改善
4.2.1 擦划伤
原因:擦划伤问题是剪切工序最常见的问题,也是最难彻底解决的问题。擦划伤产生的主要原因是由于圆盘刀或刀垫与刀轴装配时端面错出尖角,铝箔 从尖角上滑过时由于下刀或刀垫的材质比铝箔硬,在特定转速下,在极短的时间内出现极小的滑移,反映在料面上就是点状或线状擦划伤。由于大家对圆盘刀、刀垫、刀轴的加工精度和装配精度关注较多,这里 就不讨论以上原因造成的擦划伤,本文主要研究以下几种容易被忽略的情况①使用环节问题:由于圆盘刀使用一段时间后会变钝,需要经常更换新刀,而刀垫一般固定不变,每次换完新的圆盘刀都会打磨圆盘刀与刀垫的设备和质量缺陷现状描述我公司现有多台不同型号的铝箔剪切机,这些设备中既有窄幅也有宽幅,既有切边也有抽条长期累计就会造成刀垫在结合部位的外径相对变小,当一批旧的圆盘刀用完,换上一批新的圆盘刀后尖角问题就会比较突出。②设计环节问题:铝箔在分切过程中容易出现翻边和压坑, 主要原因是铝粉粘刀造成。铝粉的来源有两个,一是铝箔表面附带的铝粉;二是剪切过程中产生的铝粉。 这两部分铝粉在刀尖上聚集后使刀变钝,从而造成料面翻边,当铝粉掉落到料面上又会产生压坑。改善措施:需要经常更换新刀,而刀垫一般固定不变,每次换完新的圆盘刀都会打磨圆盘刀与刀垫的设备和质量缺陷现状。
4.2.2 翻边和压坑
原因:铝箔在分切过程中容易出现翻边和压坑, 主要原因是铝粉粘刀造成。铝粉的来源有两个,一是铝箔表面附带的铝粉;二是剪切过程中产生的铝粉。 这两部分铝粉在刀尖上聚集后使刀变钝,从而造成料面翻边,当铝粉掉落到料面上又会产生压坑。改善措施:①增加一套铝粉吹扫 装置,对刀具进行反方向吹扫,清除刀具上所附着的铝粉;②将毛毡浸满煤油、柴油等轻质油后贴靠在刀上,分切时毛毡在线擦拭刀面,防止铝粉聚集;③采用 5‰NaOH碱溶液将刀具浸泡在里面,加热到60-70℃,取出后用清水漂洗干净,擦干即可,该方法可在刀表面形成一层保护层,减少铝箔粘刀量。
4.2.3 端面错层和卷密度不均匀
原因:造成端面错层和卷密度不一致的原因主要在卷取轴上,使用气胀轴分切较重的料卷时,无论 是充气保压性气胀轴还是连续充气性气胀轴,当料卷的重量超过气压提供的支撑力时,由于料卷自重过大,会造成管芯下垂,料卷出现偏心,影响卷密度和端 面质量。改善措施:最简单的措施是及时更换刀垫,其次可采取外层包胶刀垫的结构,外径 尺寸大于圆盘刀外径0.01ram——0.05ram,高出部分为圆角,圆角半径约为0.01ram——0.15ram,,包胶为聚氨酯橡胶,硬度≥HS85。上下刀通常采用外齿轮传动方式。可以根据上刀直径变化可调整上刀传动齿轮的齿数和模数达到匹配的目的。
4.2.4跳刀和打齿
原因:跳刀和打齿是刀具使用过程中容易出现的 问题。上刀多次研磨后外径累计会减小6-8ram,仅仅依靠上下刀传动齿轮的间隙进行松紧配合,无法保证上下刀的重叠量,这样就会造 钢管芯内壁提供支撑和转矩的结构改为由轴提供交撑,由传动销提供转动力矩的结构,这两种问题出现时都会造成设备损坏并废料。改善措施:上下刀通常采用外齿轮传动方式。可以根据上刀直径变化可调整上刀传动齿轮的齿数和模数 达到匹配的目的。通过对卷 取轴进行改进,使传动和支撑功能分开,采用轴承进 行支撑可以保证轴转动时的平稳,提高分卷质量。通过采用离合器传动可以消除锥面磨损造成的频繁更换,降低设备维护成本。
5 电子铝箔的复卷
5.1 铝箔复卷机的技术要求
为了保证纸卷在运输、储存 过程中不变形、不崩裂,在印刷 设备或其他加工没备上能平稳运行,成品纸卷必须具有足够的硬度,且内紧外松、径向硬度分布均匀。因此,复卷机必需具备下列几种机能:①支撑辊转矩的置给定积分器,以使输入的速度 信号是一个平稳上升的斜坡信号, 而不是一个突变的量。改变给定积分器的积分日于问常数,即可改 变斜坡信号的E升斜率。系统启动时,转速加速度要比没有给定积分器时要小;②压纸辊压力的调节和榨制;③电力驱动的“扰性”启动和适当的速度程序控制; ④间接或肯接张力控制等。
5.2 电控系统的构成
复卷机前底辊、后底辊、退纸辊分别由单独的交流电动机驱动,纵切圆刀采用交流变频传动, 并与后底辊保持5%——20%速差。 辅助传动包括气动和液压系统两部分,分别用来控制辅助传动机 械没备的动作,配合主传动上作。 整个电控系统主要由3个部卷形态,町通过调整前后底辊的链也越小。
5.3 退纸卷张力的控制
退纸卷张力的控制影响着成品 纸卷的形态。稳定的纸幅张力能够 避免纸幅横向偏移,适当的纸幅张力能在一定程度上改善纸卷质造, 减少断头,保持复卷机稳定。因此,纸幅张力控制是电控系统的蕈 要环节。
5.4 退纸卷张力控制中的动态补偿
在系统实际运行中,退纸卷直径越来越小,由于自身惯性的作用,退纸卷在加速起卷、减速停车及稳速运行过程中,存在惯机电磁转矩应附加正的动态转矩M.,以补偿所需要吸收的能量。
6 退火制度对铝箔性能的影响
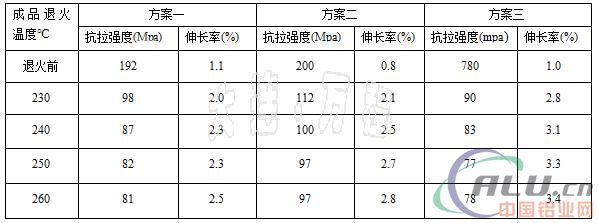
6.1 厚度对铝箔成品性能的影响
金属发生冷变形时,会使金属的内能升高,原子处于不稳定状态,自然有想稳定状态的转变趋势,大多数金属材料在室温下不肯那个完成这种转变,当金属背加热,增加原子的活动能力,加速原子的扩散速度才能完成原子向稳定状态的转变。这就是经过冷变形的金属在退火时发生会飞和再结晶的内因。但是在冷变形的金属背加热的温度给原子所提供的热能足以克服原子间的结合力,使原子发生迁移和自由扩散,才能发生在结晶,再结晶温度高低取决于原子迁移重新形成晶核和长大所需的激活能的大小,所需的激活能愈高再结晶温度也越高。方案一是将铝箔坯料在 1.5 mm 厚度时进行 中间退火(冷变形加工率约 80%),方案二是将铝 箔坯料在 2.5 mm 厚度时进行中间退火(冷变形加工率约 65%)由于按方案二生产的坯料的加工率 较小金属发生再结晶所需的激活能较高其再结晶温度也就较高其强度也就更高些遥 另一方面2.5 mm 中间退火的铝箔坯料其加工至成 根据金属学理论变形金属组织结构中主要以 位错形式保留的储存能是退火过程中再结晶的驱 动力而再结晶过程中的形核率随金属变形量的增大而增大遥 因此采用 2.5 mm 中间退火的铝箔坯料其轧制所得到的铝箔成品在退火时所经过的变形量更大以位错的形式积聚的储存 能也更大在再结晶过程中原铝箔中的形核率将大大增加从而使铝箔在成品退火后能够得到更加细小的晶粒组织,因此其强度和伸长率也就更高些。
6.2 温度对铝箔成品性能的影响
对采用铸轧法生产的铝箔坯料由于铸轧时 金属的冷却凝固和变形都是在铸轧区内完成的辊径为 650mm——700 mm 的铸轧机袁其最大铸轧区长度约50mm袁铸造区长度仅约十几毫米袁金属的凝固结晶仅在1s左右的时间内完成这种冷却凝固的速度与半连续浇铸相比约高2个数量级而铝合金中的各种杂质及合金元素在铝中的固溶度都是随温度而变化的,比如按平衡相图铁在共晶温度(655 ℃ )时在铝中的溶解度约为 0.052%室温下溶解度降为0.002%降低很多原结晶时的冷却速度愈快偏离平衡状态的程度愈严重。因此,铸轧法生产的坯料的晶内偏析及固溶体的过饱和程度都比半连续浇铸的更为严重,在中间退火时如果退火温度高(达到均匀化温度)可以促使金属中的过饱和元素充分析出,相中的固溶度减小增加了原子的自扩散系数有利于退火时新晶核的形核和长大降低了材料的再结晶温度同理如果中间退火时温度未达到均匀化效果而仅仅只能满足金属的塑性恢复则此时金属的过饱和固溶体也就未能充分析出。
因此,采用方案三生产的铝箔,在经成品退火时,在相同条件退火下更容易发生在结晶,且由于均匀化处理时境内偏析及固溶体的充分析出,材料内部形核数目的增多,材料的晶粒组织更为细小,所以成品的伸长率也就更高一些,普通中间退火的铝箔坯料轧制面成的强度更高,则是由于中间退火时温度不够,材料内部组织中晶内偏析2及固溶体的未能完全析出,对铝箔产生了固溶强化的作用,但在成品退火时如果温度继续升高,则可能由于晶粒继续长大的缘故,导致强度和伸长率急剧下降。
7 结束语
电子铝箔是一项质量控制要求比较高的产品,因此工序细节一定要重视。设备在设计、制造前期、使用过程中,维护人员要主动参与其中,将设备先天的缺陷减少到最小程度,可以为日后设备使用、维护创造有利的先决条件。
解决划伤铝带材的主要途径就是提高清洗剂的精度。根据铝箔生产的不同,所以要用到的铝箔复卷机也不一样,根据铝箔的特性提出了生产过程中所需要助于的问题。
参考文献
[1] 徐军,陈学森.我国铝工业现状及今后发展建设.轻金属,2001,(10):3-6
[2] 谢馨刚.软包装用铝的生成及质量控制.中国包装工业.1998,(12):38-40
[3] 王翠梅,焦兴贵,俞文春.铝箔退火炉的设计与应用.轻金属,2003,(12):47-50
读完这篇文章后,您心情如何?
本文网址:
/zhishi/3243.html
下一篇:铝铸件结晶的去除温度是怎么样的